June 3, 2024
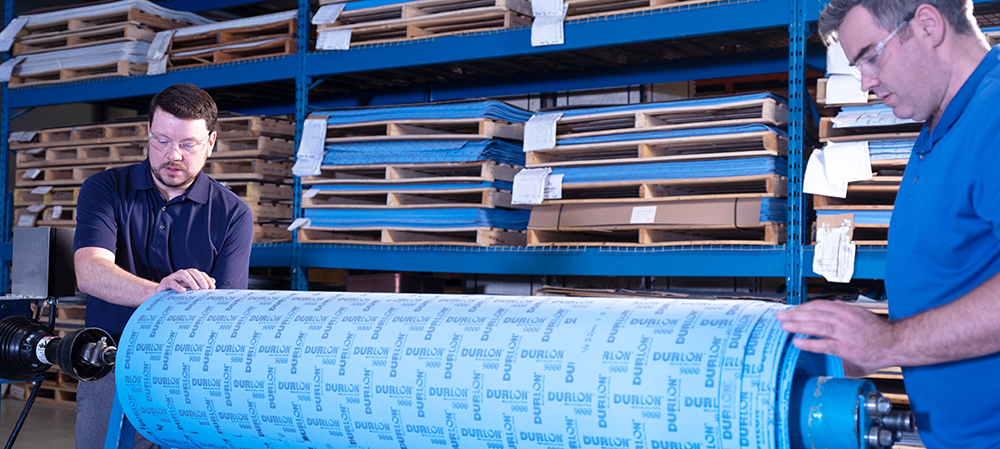
PTFE gaskets have become the gold standard for watertight, airtight, sustainable seals. Sealing components made from PTFE are used in sectors as diverse as oil and gas, chemical processing, food & beverage, marine, mining, Original Equipment Manufacturer (OEM) services, pharmaceuticals, power generation, pulp and paper, and water utilities. This article offers an in-depth look at PTFE and its sealing benefits.
What is PTFE Sheet Gasket Material?
PTFE, or Polytetrafluoroethylene, is a synthetic fluoropolymer of tetrafluoroethylene. What makes this material so useful is that it is extremely water-resistant and non-reactive. It has minimal friction and is extremely resistant to most chemicals, including those that are known for their corrosive properties. The primary qualities of PTFE gasket material include:
- Temperature Resilience: PTFE gaskets are made to resist extreme temperatures, ranging from -212°C to 260°C.
- Chemical Resistance: PTFE can withstand even the most aggressive substances, which makes them ideal for any industrial processes that involve the use of corrosive chemicals.
- Low Friction: PTFE has an extremely low coefficient of friction, making it ideal for applications where a non-stick surface is required.
- Electrical Insulation: PTFE has high insulation resistance and a low dielectric constant of 2.0. As a result, these gaskets do not conduct electricity and are perfect for applications where electrical insulation is an important requirement.
- Non-adhesive: PTFE has a low coefficient of friction and a non-stick surface, preventing materials from adhering to it.
The Benefits of Using PTFE Gasket Sheet Material
Due to the characteristics listed above, PTFE is an extremely effective sealing solution for several applications. Its benefits include:
- Uses across a wide temperature range: From sub-zero conditions to temperatures approaching 500°F (260°C), PTFE gaskets provide dependable sealing of an extremely high standard.
- Compressibility and conformability: PTFE is versatile and adaptable. PTFE gaskets can be adjusted for uneven flange surfaces.
- Electrical safety and insulation: In applications where electrical isolation is important, PTFE gaskets are the best choice.
- Easy cleaning and non-stick properties: These gaskets are extremely easy to clean and maintain.
- Non-toxic: PTFE gaskets are suitable for food, beverage, and drinking water applications.
- Versatile: Gaskets made from PTFE sheets are used in a broad array of industries, creating reliable and versatile sealing in all kinds of applications.
Different Types of PTFE Gaskets
Durlon manufactures seven different types of PTFE gaskets:
- Durlon® 9000 is for use in general industrial applications where resistance to highly aggressive chemicals is required. In addition, the shape of the fillers does not allow wicking which can cause corrosion on flange surfaces.
- Durlon® 9000N is also designed for general industrial applications where resistance to highly aggressive chemicals is required. In addition, the shape of the fillers does not allow wicking, which can cause corrosion on flange surfaces.
- Durlon® 9002 is an adaptation of the original glass-filled formula to better meet extreme cryogenic demands and is readily available through the standard manufacturing process and requires no secondary heat or cleansing treatments prior to gasket cutting.
- Durlon® 9200 is a filled PTFE gasket material used where resistance to highly aggressive chemicals is required. Barium sulfate fillers are homogeneously blended with pure PTFE resins to give Durlon® 9200 its physical and mechanical properties.
- Durlon® 9400 is a high performance filled PTFE gasket material designed for use in piping and equipment, chemical, and other general industrial applications where resistance to highly aggressive chemicals (including hydrofluoric acid) is required. Durlon® 9400 can also be used as the gasket of choice for anhydrous hydrogen fluoride (AHF) in railroad tank cars and a good alternative for use in plants where barium sulfate filled PTFE may not be suitable.
- Durlon® 9600 is a biaxially expanded PTFE gasket, made with only pure PTFE resins, designed for use in process piping and equipment, in chemical, pulp and paper, food and beverage, and other general industrial applications, where resistance to highly aggressive chemicals is required. Durlon® 9600 is also suitable for sealing flanges with irregular surfaces. It will not exhibit the cold flow problems associated with virgin PTFE, or the hardness problems of some filled PTFE products.
- Durlon® Virgin PTFE gasket material is a high-performance PTFE product designed for use in piping and equipment in chemical and other general industrial applications where resistance to highly aggressive chemicals (including hydrofluoric acid) is required.
How to Choose the Right PTFE Gasket Material for Your Needs
When choosing a PTFE gasket sheet material, several factors need to be considered to ensure it meets the specific requirements of your application. Here are the key considerations:
Chemical Compatibility
Chemical Resistance: Assess the chemical environment the gasket will be exposed to. PTFE is highly resistant to most chemicals, but you should ensure it can withstand the specific chemicals in your application.
Temperature Range
Operating Temperatures: Determine the minimum and maximum temperatures the gasket will experience. PTFE performs well across a wide temperature range, but verifying its suitability for extreme conditions is crucial.
Pressure Conditions
Pressure Levels: Evaluate the operating pressure. PTFE gaskets can handle a range of pressures, but high-pressure applications may require reinforced or filled PTFE materials.
Mechanical Properties
Strength and Durability: Consider the mechanical stress the gasket will endure. Ensure the PTFE material has the necessary tensile strength and compressive properties.
Sealing Performance
Leakage Prevention: Ensure the gasket material provides a tight seal to prevent leaks. This is especially important in applications involving hazardous or valuable substances.
Thickness and Size
Dimensions: Choose the appropriate thickness and size for your application. The thickness can affect the gasket’s ability to seal and its overall performance.
Surface Finish and Flatness
Surface Requirements: Ensure the gasket’s surface finish and flatness match the flange or surface it will be sealing against. Imperfections can compromise the seal.
Compliance and Certifications
Industry Standards: Verify if the PTFE gasket material complies with relevant industry standards and certifications, such as FDA approval for food and pharmaceutical applications.
Durlon is one of the most recognizable brands when it comes to sealing solutions. We manufacture a wide variety of gaskets of different types, suited for several industrial applications. Contact us for more information about our PTFE gaskets.