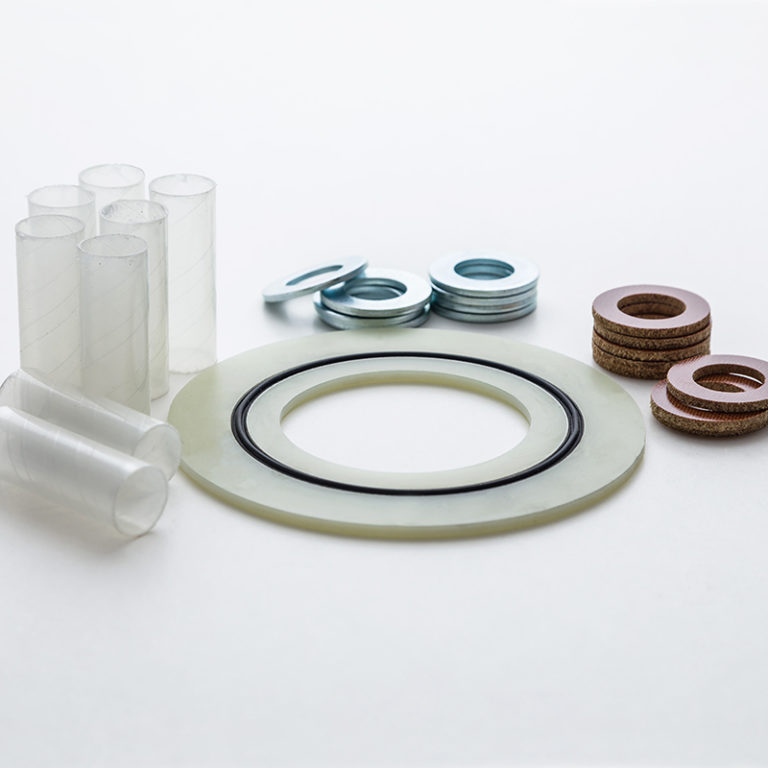
Durlon® iGuard™ EN
Durlon® iGuard™ flange Isolation and sealing systems consist of all the necessary components to seal and electrically isolate between flanges, from general service to severe service applications. Gaskets are available in Raised Face (Type F), Full Face (Type E) and RTJ (Type D) flanges from NPS 1/2” (DN15) to NPS 144” (DN 3600) or equivalent, to meet all international piping sizes.
iGuard™ EN: The iGuard™ EN style isolation gasket is manufactured from Nema grade G-10/FR-4 glass epoxy material incorporating a Viton double-ogee sealing element. This kit comes standard with one iGuard™ EN gasket, two isolating Nema grade G-10 washers, two SAE Zinc plated backup washer, and one Nema grade G-10 sleeve tube for every bolt/stud. Maximum pressure class - 2,500# ANSI, 10,000# API.