Updated Durlon Literature!
Exciting news! We’ve updated our Durlon Gasket Manual, adding CGIs (computer-generated images) that showcase our products in a way that’s visually appealing and highly accurate to ensure ease of navigation with refreshing visuals. Check it out here.
We are continually rolling out exciting new content: the “Pros and Cons of Expanded PTFE Gasketing” blog, “High-Temperature Sealing” literature, and the release of the final 2 parts of our 3-part SEALutions video series “Kammprofile and Spiral Wound Gaskets”.
Lastly, be sure to stay tuned as we go live with our new “Industry Applications” literature that explains the production flow processes and where Durlon products are best used.
More to come in the next issue!
Austin Boyd, Marketing Coordinator
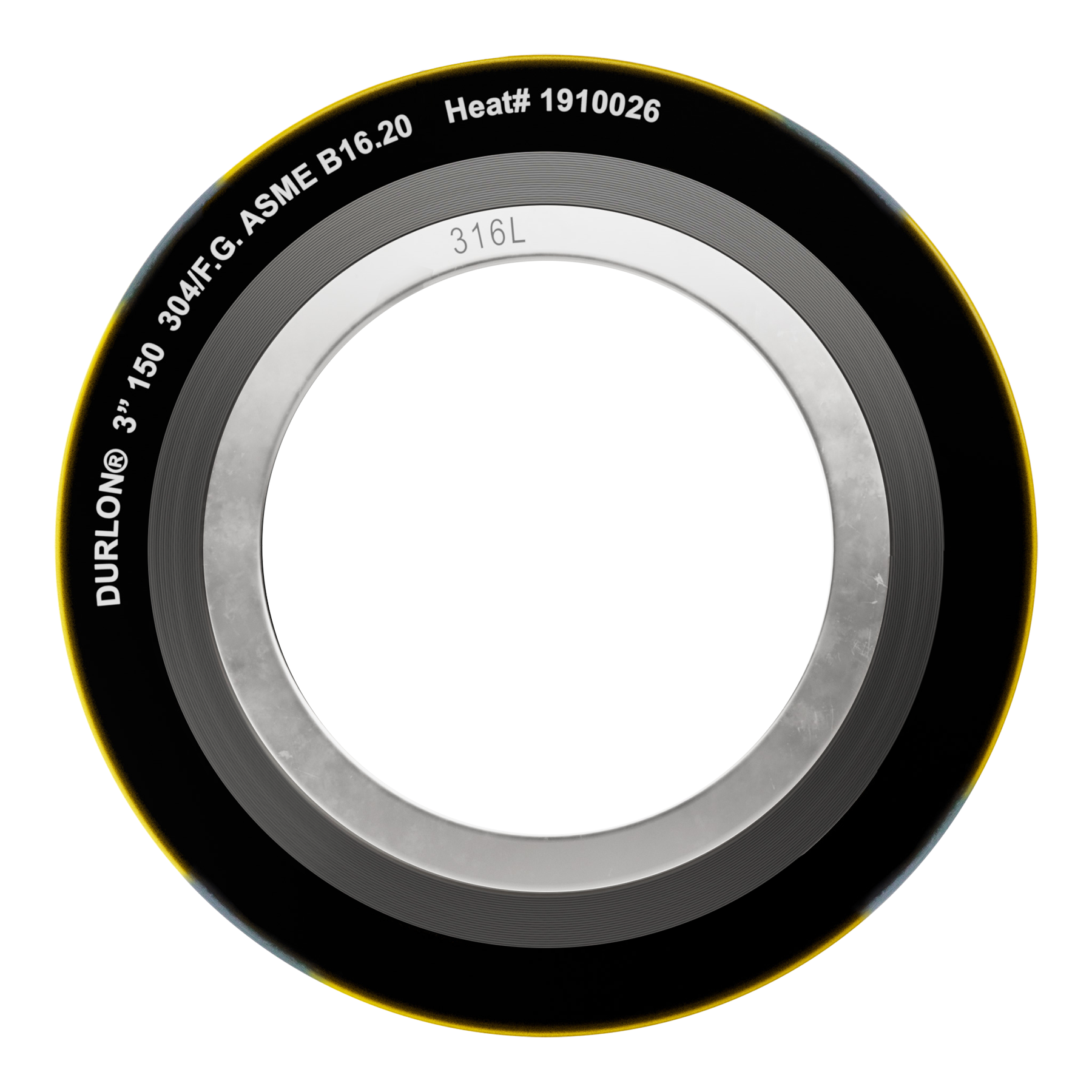
Click on the button to toggle between showing and hiding content.
Featured Product – Durlon®Spiral Wound Gaskets
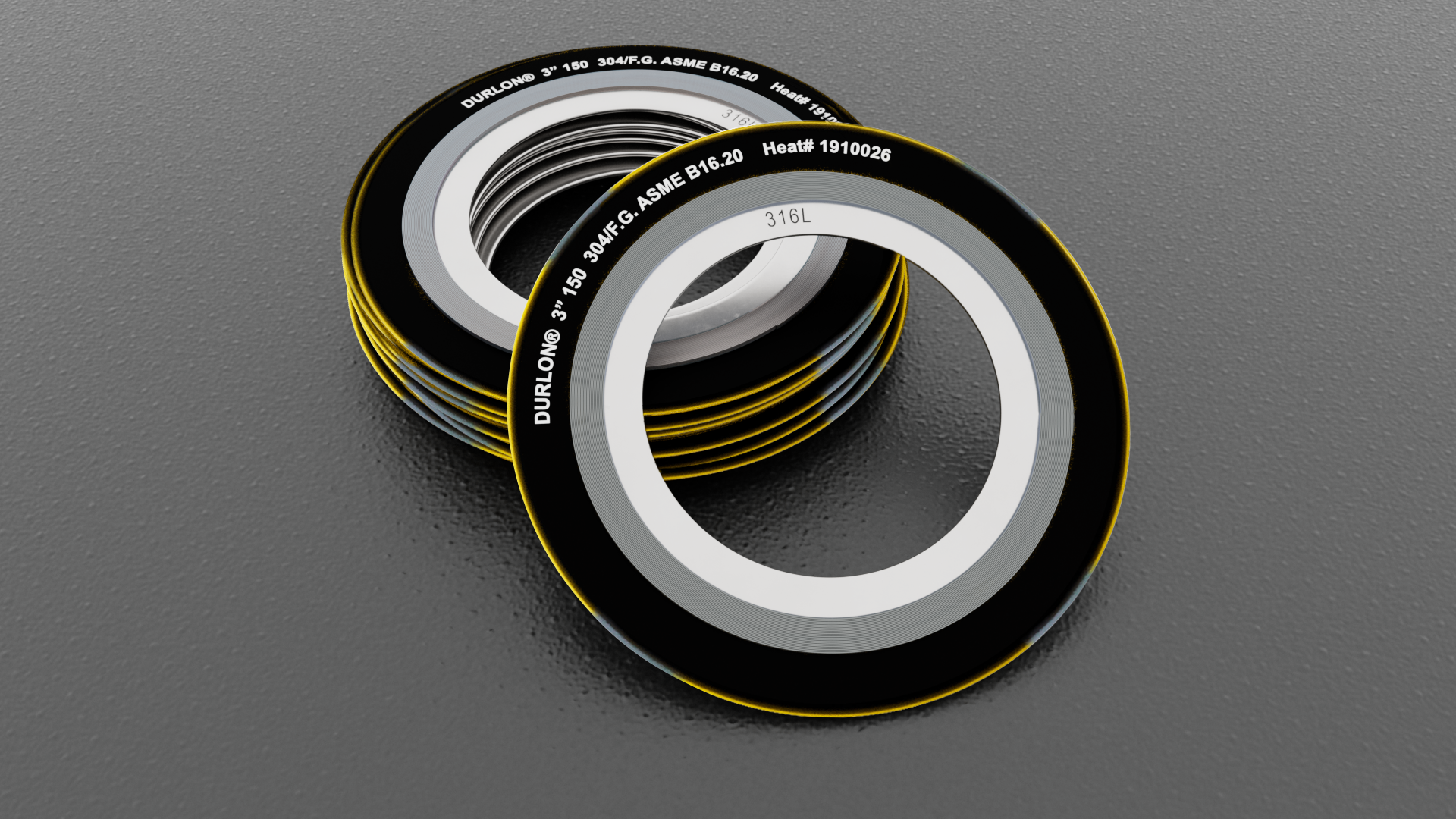
Durlon® Spiral Wound Gaskets
Are made with an alternating combination of a preformed engineered metal strip and a more compressible filler material which creates an excellent seal when compressed. The engineered shape of the metal strip acts as a spring under load, resulting in a very resilient seal under varying conditions. The strip metallurgy and filler material can be selected to seal a wide range of applications. All Class 150 and 300 Durlon® SWG styles have been engineered to precise manufacturing tolerances and utilize optimal winding density that allow for lower stress (bolt load) sealing compared to conventional spiral wound gaskets thus eliminating the need to stock both standard and low stress SWG’s.
Style D
• Sealing element only consisting of preformed engineered metal and more compressible filler material.
• Commonly used in tongue and groove or male and female flanges.
• Can also be supplied with an inner ring as Style DI.
Style DR
• Sealing element (D) combined with a centering ring (R) which reinforces the gasket and acts as a compression stop.
• Commonly used with standard raised face and full face type flanges.
• Centering ring is epoxied which provides superior corrosion resistance compared to powder or liquid coating.
Style DRI
• Sealing element (D) combined with a centering ring (R) and an inner ring (I) which improves radial strength and protects the sealing element from erosion and inward bucking.
• Commonly used with standard raised face and full face type flanges.
• In accordance with ASME B16.20-2012, inner rings for all gaskets are recommended for all sizes, materials and classes.
Industry Applications:
• Chemical Processing
• Food and Beverage
• General/Heavy Industry
• Mining
• Oil and Gas
• Petrochemical
• Power Generation
• Pulp and Paper
• Refining
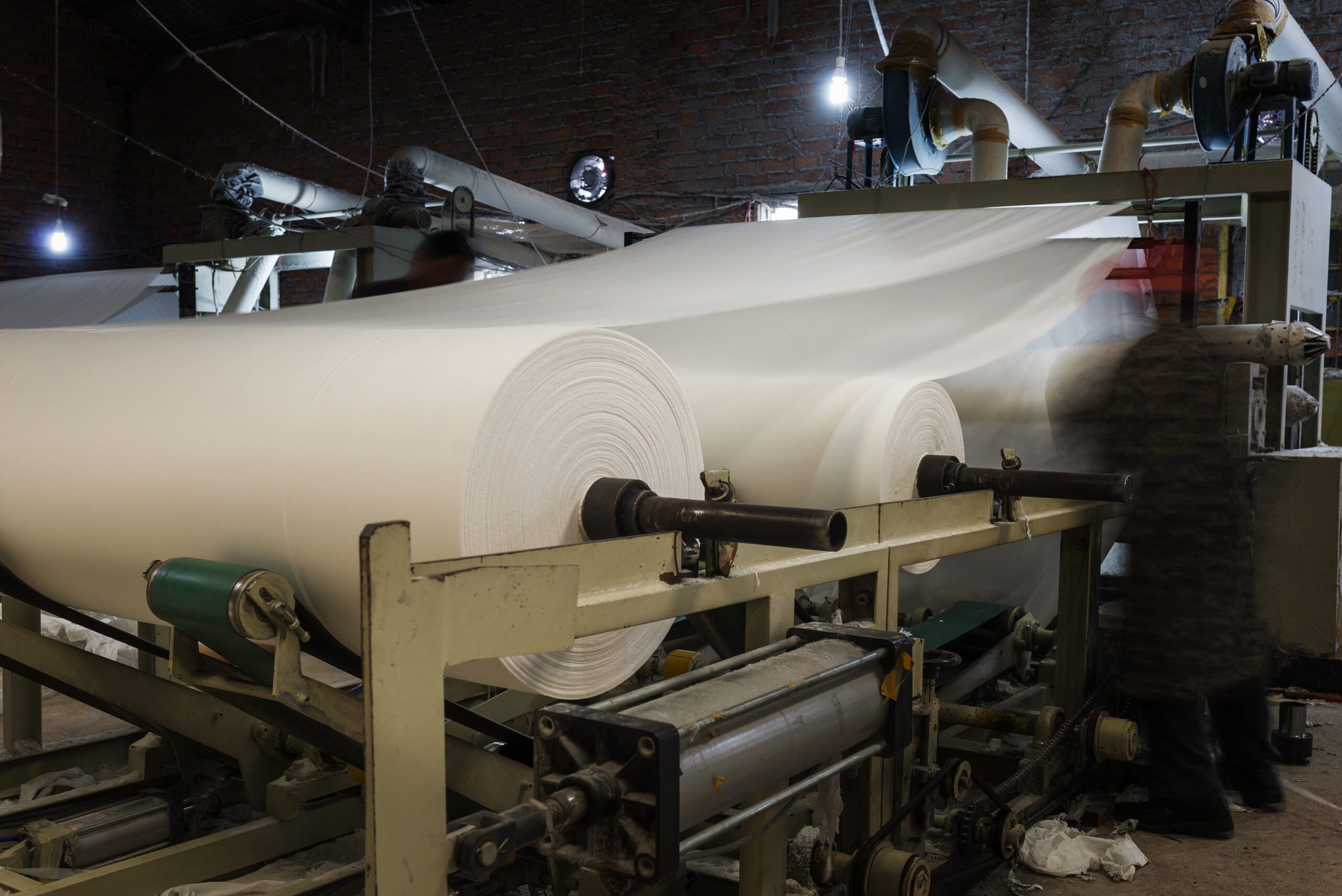
Click on the button to toggle between showing and hiding content.
Featured Industry – Pulp And Paper
Pulp And Paper
The history of the pulp and paper industry dates back to ancient times, with evidence of papermaking in China dating back to the 2nd century BCE. The process was later introduced to the Arab world in the 8th century and then to Europe in the 12th century.
Today, the pulp and paper industry is a global industry with a wide range of products and applications, including packaging, printing and writing paper, tissue paper, and specialty papers. The industry continues to evolve and innovate, with new technologies and processes being developed to meet the growing demand for sustainable and environmentally responsible paper products.
Here is a brief example of the various processes involved in the pulp and paper industry:
The first step in papermaking is the production of pulp. Pulp is typically made from wood chips, which are first debarked and then chipped into small pieces. These wood chips are then boiled in a mixture of chemicals and water in a process known as the Kraft process. This process helps to break down the lignin, a natural substance that binds the wood fibers together, and separates the fibers from the other components of the wood. Once the fibers are separated, they are washed and bleached to remove any impurities and to achieve the desired level of whiteness.
Once the pulp has been produced, it is ready to be turned into paper. The papermaking process starts by mixing the pulp with water and additives such as sizing agents, which help to control the paper’s properties. This mixture is then fed into a machine known as a paper machine, where it is formed into a continuous sheet of paper.
The paper machine consists of several parts, including the headbox, the wire section, the press section, and the dryer section. The headbox is where the pulp mixture is introduced onto the paper machine. The wire section is where the water is removed from the pulp, and the fibers start to bond together to form the paper sheet. The press section is where the paper is squeezed between two large rollers to remove even more water and to increase the paper’s density. Finally, the dryer section is where the paper is dried using a series of steam-heated cylinders.
After the paper has been produced, it may be further processed to improve its properties. For example, it may be coated with a layer of clay or other materials to make it smoother and more resistant to ink. Alternatively, it may be calendered, which involves pressing the paper between rollers to make it smoother and more even. Finally, the paper may be cut into sheets or rolled into large reels, ready for shipping and use in various applications.
Chemical Recovery
Alongside paper production is a process known as chemical recovery; recycling and reusing byproducts of the initial paper production process.
Black liquor:
Black liquor is a by-product of the papermaking process that contains dissolved wood lignin (organic polymers) , hemicellulose, and other extractives from the wood. It is a dark brown liquid that is rich in organic matter and has a high pH. The black liquor is collected and sent to the process for the recovery of the chemicals.
Evaporator:
The evaporator uses heat to remove water from the black liquor, resulting in a concentrated liquor called weak black liquor which is then sent to the recovery boiler for further processing.
Recovery boiler:
The recovery boiler is used to burn the concentrated black liquor from the evaporator to recover inorganic chemicals, such as sodium hydroxide and sodium sulfide, used in the papermaking process. The recovery boiler produces steam and electricity, which are further used in the paper mill.
Caustification:
A process in which the weak black liquor from the evaporator is treated with calcium oxide (lime) to convert the sodium carbonate in the liquor to sodium hydroxide. The caustification process produces a white slurry called white mud, which is then sent to the clarifier for separation.
White liquor:
A solution of sodium hydroxide and sodium sulfide that is used in the papermaking process to separate wood fibers from each other.
Industry Trade Shows
Canadian Mining Expo – June 6-8, 2023
A well recognized trade show in the mining industry, attracting international delegations and mines representing the central parts of Canada.
McIntyre Community Center
Timmins, ON, Canada
Hydrovision International – July 11-13, 2023
Hydrovision International® is the largest hydropower and dams industry event worldwide.
Charlotte Convention Center
Charlotte, NC, USA
Offshore Technology Conference (OTC) – Aug 16 – 19, 2023
Where energy professionals meet to exchange ideas and opinions to advance scientific and technical knowledge for offshore resources and environmental matters.
NRG Park
Houston, TX, USA
Next issue highlights: Industry and product focus. We’ll share a new video, news, and upcoming events you may want to look into. And of course, we will put those genius brains to the work again and tickle your funny bone with another adventure from our gasket guru. See you in August 2023!